Revolutionary shaft sealing technology
Tamar shaft sealing Technology
​
Tamar shaft sealing technology combines all of the benefits of the conventional sealing methods to create a synergetic solution that contains eight layers of protection against leakage.
The result is Zero leakage even under extreme conditions of slurry and run-outs.

Tamar shaft seal in the S.O.I.P.C test
​
A. Sealability – The Tamar shaft seal with eight protection layers provides zero leakage even under
extreme run-out and slurry environments.
B. Operational Flexibility – The Tamar shaft seal does not include any ceramic or silicon materials and it is an almost infallible solution. Even when the environment goes way beyond the limits of the seal, the seal will continue to work even if in a partial manner to prevent toxic emissions and costly downtime.
C. Independent – The Tamar shaft seal is a dry - running seal and uses a separate cooling jacket for
cooling. It operates without impacting the process it is designed to protect.
D. Predictability – The Tamar shaft seal has a built - in mechanism that provides operators with an early warning of around 3 – 4 weeks before a sealant refill is required.
As long there is some sealant in the stock, a positive pressure is maintained preventing pressure drops and leakage. Adding sealant is done on line and does not require production shut down.
E. Cost – The cost of the Tamar shaft seal is within the range of a mechanical seal. However, the huge
advantage of the Tamar shaft seal is its ability to minimize production down-time, adding only a very
small maintenance cost. This combined with dry-running operation; minimal on-site maintenance
means an excellent cost-effective sealing solution.
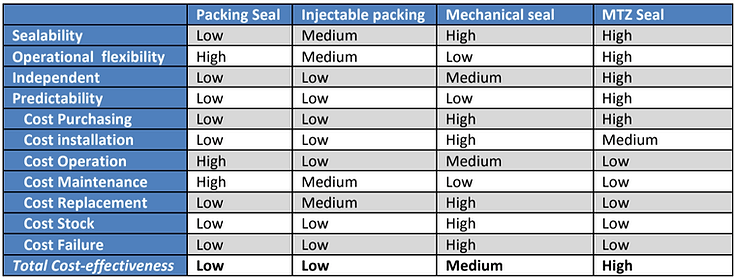